CSR Initiatives
Creating products focusing on environment
Our goals for "creating products focused on the environment"
Our products
Bio Paint
This paint uses a mixture of plant-based raw materials, which had been difficult to use due to performance and price. It is equivalent to paints used for car interior parts and home appliances, and has the potential for a wide range of applications.
This product reduces the amount of fossil fuel-based resources used, triggers the start of using plant-based resources rather than fossil fuel-based resources, and may reduce CO2 emissions.
Currently the composition ratio of plant-based raw materials in coating films is a maximum of 40%. Our goal is to increase this ratio to 100%.
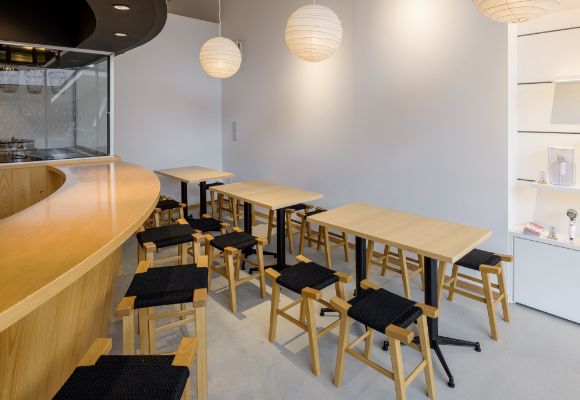
Our Bio Paint is used as the finishing coat for a table made of Japanese cypress.
Our group addresses environmental issues such as fuel materials, CO2, VOC, energy, and health and offer multifaceted values in coating materials. One of our initiatives is Bio Paint, which decreases the shortage risks of fossil fuel-based raw materials. We will continue to explore the possibilities of using plant-based raw materials to replace fossil fuel-based raw materials and will continue to share with society to reduce CO2 emissions and to address energy issues.
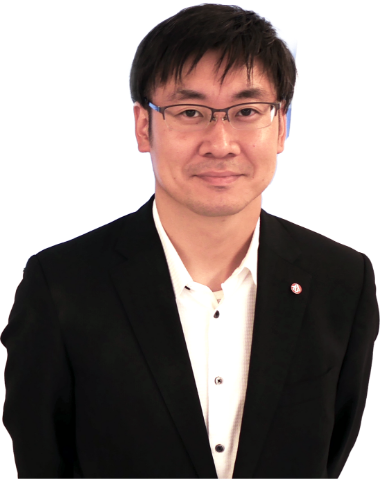
Manager
In-mold coating
This product is used in systems that inject a coating as plastics are being molded.
While there are many ways of coating, it is typical in the plastic-molding market (where most of our products are used) to spray on coating due to the shape of the molds, facilities, and associated costs. However, not all of the spray coating adheres to the target, generating waste in the form of mists. When coating includes solvents, these wastes could generate VOC, which can lead to environmental issues.
We took interest in the in-mold coating technology for plastic manufacturing developed in Europe, proposing this technology to our customers as to resolve the above problems. We developed a coating that was optimal for this application method.
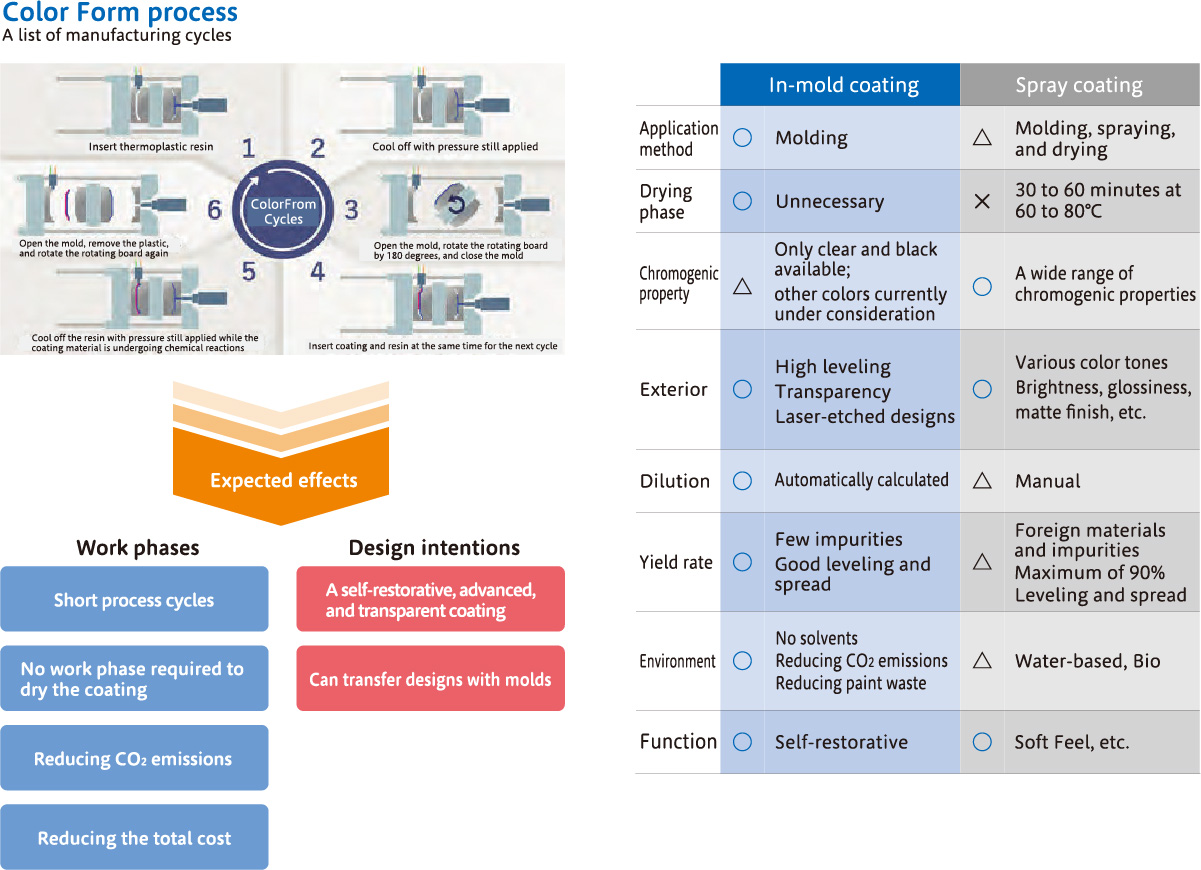

In-mold coating technology has attracted attention as a promising solution for a sustainable society due to its possibilities in cost and workload reduction, its solvent-free properties, and as an effective method of reducing CO2 emissions. To establish this manufacturing/coating method, we must simultaneously develop facility equipment, molds, and coating materials. We will work with our business partners to spread the use of in-mold coating and contribute to a sustainable society.
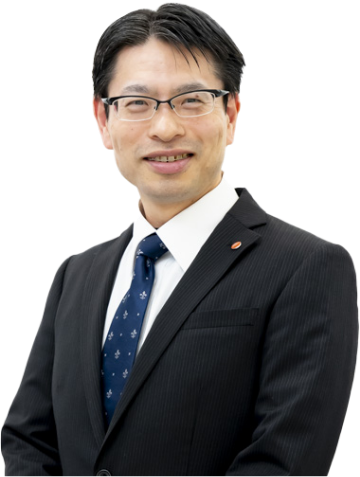
General Manager
Plating coating system: Indium coating
Typically, plating and evaporation coating methods are used to apply functional designs to mirror faces. However, plating has a high environmental load because it requires waste water treatment, and evaporation is not suitable for continuous line production because it requires a special facility and must be executed in batches. Conventional plating coatings (silver mirror finishes, colloidal silver, and silver complexes) do not resist weather or corrosion well.
Indium coating, which has advanced features in both design and function, is the solution to these challenges. We’ve also co-developed a controlled plating spray coating with TAKUBO Engineering Co., Ltd.
We established an advanced production system based on indium coating spray.
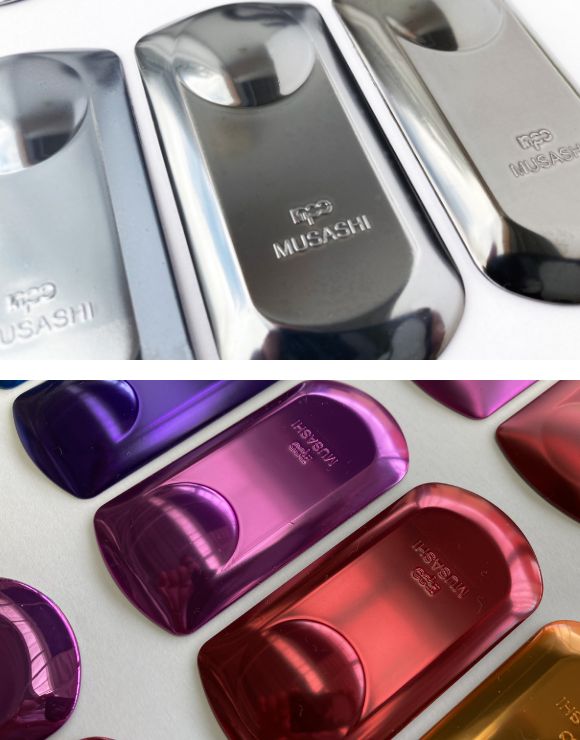
We applied functional designs to mirror faces without having to implement waste water treatment or large-scale equipment with a plating spray coating system. We will continue to develop an advanced environmentally-friendly system that alleviates environmental loads and reduce costs.
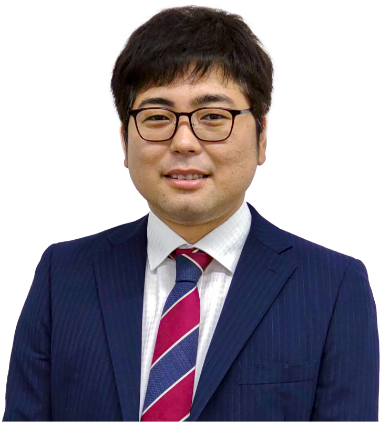
Manager
UV curable paints may alleviate environmental loads with existing water-based paints
There are many types of paints, each with advantages and disadvantages. Paints are selected based on usage, the shapes the paint will be applied to, and coating equipment.
To alleviate the environmental loads of our paint users, we offer paints that are different from conventional paints and take initiatives on environmental issues.
Thermal hardening paints => UV curable paints:
Reducing the amount of energy utilized during film formation
By switching from thermal hardening paints to UV curable paints, it is possible to reduce 50-70% of electric consumption from the energy used for film formation.
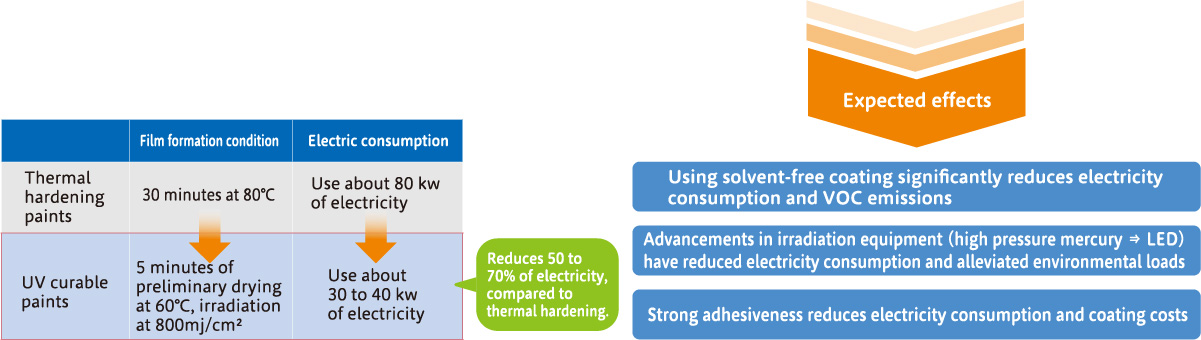
The primary cause of global warming is CO2 emissions. UV curable paints conserve energy during the process of drying the coating and significantly reduces CO2 emissions. It is predicted that there will be great demand for such paints.
We would like to resolve societal issues by developing advanced paint products (such as UV curable paints) and incorporating technological innovations to develop adhesive coating systems and irradiation systems.
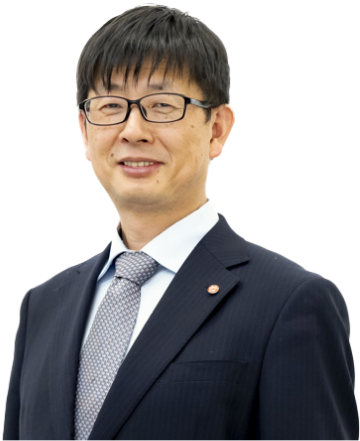
Manager
Solvent-type paints -> Water-based paints: Reducing VOC emissions
Switching from solvent-type paints to water-based paints can reduce VOC emissions.
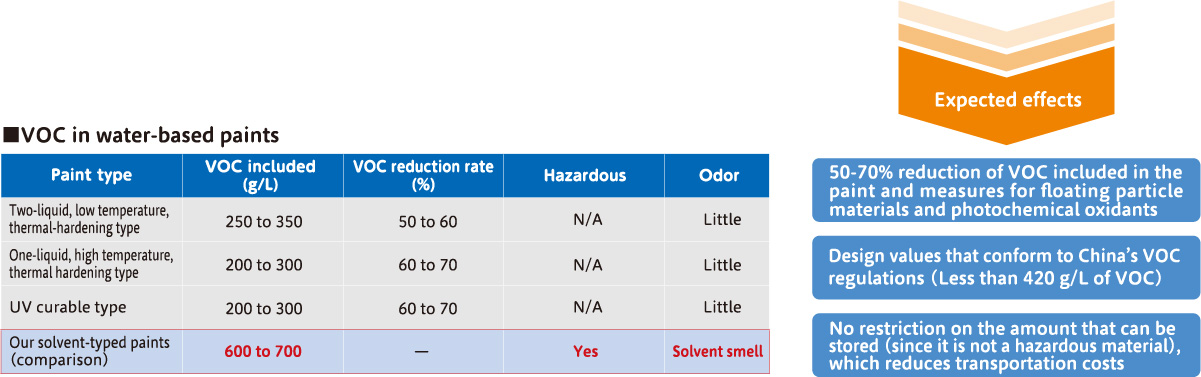
Initiatives to reduce VOC emissions with water-based paints started in the 1960s with coating of car exterior parts and electrodeposition paints. It was developed and mass-produced for construction, containers, heavy machinery, and other fields. Our group is devoted in the development of water-based paints that can be applied to plastics, which requires various coating film functions. We strive to develop paints which meet the environmental criteria of different countries.
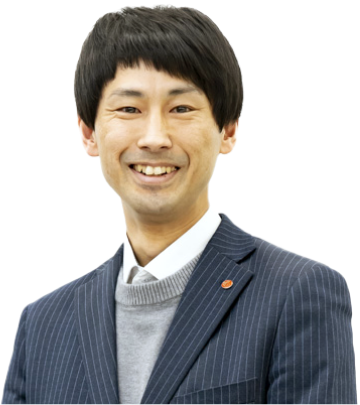
Manager
Our Research & Technical Development Division is committed to applying unique ideas to develop merchandises that contribute to society. We will leverage our development capabilities across our global network of Japan, China, South Korea, ASEAN, India, and Hungary to enhance our lineup of environmentally-friendly merchandises. We will continue to operate as a paint manufacturer contributing to a sustainable society.
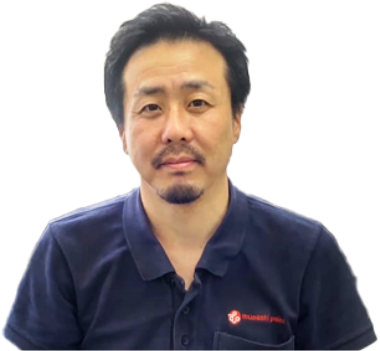
Division General Manager